Print Essentials
Have you ever wondered how the digital files you sent to your printer became a finished product? This section of the website takes some of the mystery out of the process with a crash course on the ABC's of printing and helps you make the right decisions for your particular goals and needs.
General Lexicon
There is much terminology to learn in the printing industry as there are so many facets to printing and because technology keeps changing in this digital age. Here are easy-to-understand definitions for common printing terms.
Sheetfed Press: a press that feeds and prints individual sheets of paper rather than continuous rolls used by web presses. Sheetfed presses come in a variety of sizes from very small units that one might find in a quick print shop to very large presses used for longer run and larger format needs. They can print on a variety of substrates including paper, plastics, metal and other materials. Sheetfed presses also come in a wide range of colour configurations and some are equipped with perfecting units, which enable the printing of both sides of the sheet in a single pass.
Web Press: a press in which a continuous roll (web) of paper or other substrate is fed through the printing press. Particularly in the case of web offset printing, a wide range of equipment can be attached to enable roll-to-roll finishing, sheeting, signature folding or a variety of in-line finishing techniques including perforating, gluing, die-cutting, folding and other options. Web presses are better suited to high-volume publications such as mass-market books, magazines, newspapers, catalogues and brochures, as well as direct mail.
Heatset Process: heatset web offset printing is a printing process in which ink is dried rapidly by forced-air heating. In reality, the ink is not fully dried after the web of paper passes through the ovens. Rather, oil-based solvents reach evaporation point leaving waxes, resins and pigment. The paper next passes through chilling rollers where the waxes and resins cool down and set. Finally, a layer of silicone is applied to prevent the ink from offsetting onto other parts of the press during any finishing processes. Moisture may also be added to the paper to replace what was lost in the ovens.
Coldset Process: coldset web offset printing dries the ink purely through evaporation combined with absorption into the paper. It is suitable only for uncoated, supercalendered and matte finished papers, which allow sufficient ink absorption. The majority of newspapers globally are printed on coldset presses, along with many forms, manuals, books and other products suited to uncoated papers.
Signature: a group of pages that are printed on both sides of a sheet of paper and then folded and trimmed to the finished page size. The number of pages within a signature depends upon your page size and the dimensions of the press sheet used. Publications may have multiple signatures that are gathered and trimmed on saddle stitching or perfect binding machines.
To learn more, contact us.
Graphic Production Chain
There are four main steps in producing a printed project. We've outlined them below:
1 - Conception: developing a project management plan and defining project goals/scope, design and framework. You're probably most familiar with this step, which involves a start-to-finish project plan, but you may not realize the value of bringing your printer and other suppliers like packaging and fulfillment specialists into the process. For example, you'll want to ensure that everything from the project's dimensions to paper selections is best suited to the equipment you'll be using and the end use of the materials. Mistakes can be costly, both in terms of aesthetics and your budget. Even areas like fulfillment, warehousing and distribution can't be afterthoughts if you want to lower costs and optimize results. They need to be part of the upfront discussion that includes such tasks as creative development and campaign execution.
2 - Premedia: processes and procedures that occur between the conception of original artwork and the manufacturing of final output channel; often referred to as prepress in the print medium. Today premedia is increasingly shared between the client and the printer. While you don't want to take on more responsibility than you can efficiently handle, you'll miss out on savings (and increase your headaches) if you don't learn how to create error-free, print-ready PDF files and keep your monitors and printers calibrated so that you see more accurate colour representations of your work.
Depending on the type of presses used, the prepress workflow could include the following steps:
Content creation, where page geometry, image attributes, colour management, graphics, text and transparency parameters, among others, need to be considered as per the press used to print the final product.
PDF (Portable Document Format) creation, where Adobe Acrobat is used to generate all the elements of a design file as an electronic image that you can view, share and ultimately print as a CMYK file on virtually any printing device. PDF uses the PostScript printer description language and is also highly portable across computer platforms. The industry uses PDF as its default standard, since it's an open standard for document exchange.
File submission to the printer.
File refine, where the files are preflighted, trapped and colour optimized. By preflight, we mean checking for anything in the file build that will affect the runability of the file.
Proofing of files, where we can accurately predict colour output based on industry profiles and colour management best practices. A printer can either provide a hardcopy or a virtual proof to its customer for approval.
Imposition, which is the process of arranging pages correctly prior to printing so that they fold in the proper sequence. The imposition is chosen based on the project page count, page size and binding method.
Imposition proofing by customer.
Plate imaging, where an image is burned onto an aluminum plate, which then transfers the imposed pages to the press and ultimately the paper. Printers need to create four plates to form an image (one plate per CMYK colour.
3 - Press: production machines falling into two major categories:
plate system machines (such as offset lithography, flexography and gravure printing)
plateless system machines (ex.: digital printing presses)
Offset Lithography: By far the leading printing process, offset presses come in sheetfed and web. Offset presses have three printing cylinders (plate, blanket and impression) as well as inking and dampening systems. As the plate cylinder rotates, the plate comes in contact with the dampening rollers first, and then the inking rollers. The dampeners wet the plate so that the non-printing areas repel ink. The inked image is then transferred (offset) to the rubber blanket and paper or other substrate and is printed as it passes between blanket and impression cylinders. Offset produces a smooth print without embossing an ink ring or serrated edges that are characteristic of flexography and gravure, among others.
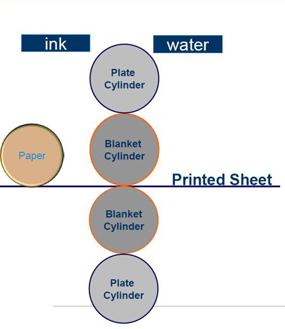
Uses: Offset process is used for a wide range of materials including books, magazines, catalogues, newspapers, flyers, brochures, folding boxes, posters and art reproductions. Whether you use sheetfed or web depends on a variety of factors including run length, dimensions of your piece and substrate used.
Flexography: This is a form of rotary web-relief printing using flexible rubber or resilient photopolymer relief plates and fast-drying, low-viscosity solvent, water-based or UV inks. Flexographic presses are web-fed in three types: stack, in-line and central impression cylinder. An advantage of flexography is that it can print virtually any substrate that can be put into roll form. It is adept at printing large areas of solid colour with high gloss and brilliance.
Uses: This process covers a wide range from printed toilet tissue to bags, pressure sensitive labels, flexible packaging like potato chip bags, corrugated board and materials like cellophane, polyethylene and other plastic films.
Gravure: This process involves engraving the image onto the cylinder of a rotary printing press, which serves as an image carrier. The recesses are filled with ink and the raised (non-printing) portions of the plate or cylinder are wiped or scraped free of ink leaving the ink only in the recesses. The paper or other material is pressed against the inked plate or cylinder and the image is transferred to the paper. It can produce fine, detailed images and can be used for short- or long-run printing. Because it can carry more ink to the substrate than other processes, it is known for its remarkable density range. Costs can be significantly higher than other printing processes.
Uses: Newspapers, magazines, catalogues, fine art and photographic reproductions, postage stamps, corrugated packaging and printed electronics can all employ gravure printing.
Digital Printing: This category enables the creation of images directly on plateless presses. Among the most popular methods are inkjet and laser printers that deposit pigment or toner onto a wide variety of substrates ranging from paper to canvas, photo paper, glass, metal, marble and many other materials. A great advantage of digital printing systems is that many enable 100% variable text and images on every piece, thus allowing one-to-one customization and greater response rates. Digital printing eliminates many steps in the premedia process and also requires very short makereadys, which make them suitable for on-demand scenarios. Nonetheless, they have dimensional volume limitations.
Uses: Digital printing can be used for books, manuals, specialty publications, direct mail, labels, promotional billing statements, coupons, photos, photo books, yearbooks, fine art prints, menus, brochures, stationary, business cards, greeting cards and small signage.
4 - Postpress. Perhaps the most important lesson about the postpress area is that decisions you make in the planning process can have a big impact on finishing. Lots of things come together here, including collating, binding, trimming, inserting, die-cutting, adding a flap on the cover, personalizing, applying involvement devices and packaging. Every design decision can definitely influence both the appearance of your piece and the cost.
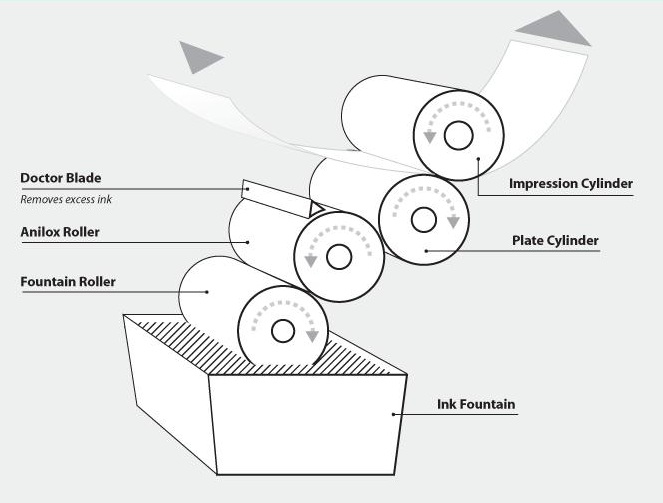
File Preparation Basics
Because of the many variables in high-speed printing, there is an inherent margin of error in the printing and finishing processes. Thus it is important to respect your printer's specifications regarding trim size, bleeds, type safety and registration offset instructions to minimize risk and ensure product excellence.
A good first step is to use a preflighting software such as Enfocus, Job Assistant (TC Transcontinental's software) and other solutions. Although the printer will almost certainly preflight your files upon receipt, you can save yourself time, headaches and potential expense by sending them correctly the first time. When you consider that industry studies have shown that nearly half of all supplied files have problems (#1 problem is missing fonts), it's worth the effort. Another good practice is to send a test file to further ensure you are complying with your printer's requirements.
Key terms:
- Trim. Finished size of the printed piece after trimming.
- Bleed. Page elements that extend beyond the trim, allowing the ink to reach the end of the sheet after final trimming.
- Type Safety. A zone or margin inside the page trim designated to assure live copy or graphics do not trim.
- Crop Marks. Printed lines indicating where trims are to be made.
- Registration Offset. The distance that the crop marks are offset from the trim.
To learn more, contact us.
Print Formats
There are numerous print formats, and you will find below definitions of the most common ones. Which one to choose depends on a variety of factors including the amount of information to be included, the impression you want to make on your audience and your budget.
Digest Format: a generic term used to describe several smaller than conventional sizes for magazines and catalogues. Most often they are approximately 5½" by 8½". Perhaps the most famous digest-size magazine is Reader's Digest and the most famous catalogue is the Avon Products. The size is considered easy to tote and may offer some postage-cost advantages.
Slim Jim Format: a catalogue format that measures up to 6.125" x 11.5" and qualifies for lower "letter" rates from the U.S. Post Office. To qualify, however, they must also be 3 ounces or less and be sealed.
Magazine Format: the most common and economical magazine format is 8 3/8" x 10 7/8", because it best fits most press and bindery equipment with minimal paper waste. The cost per inch for larger and smaller magazine formats is generally higher. This format is also called ''quarter fold'' or ''upright''
Tabloid Format: a size of newspaper page that is approximately 14" high by11" wide, or half the size of a standard broadsheet page.
Broadsheet Format: the most common newspaper format, which is typically 11" to 12" wide and 20" or more in height.
Stepped Format: this can include stitched formats as well as inserts placed in a pocketed folder. On a stitched brochure, each of the four page signatures is a different width but with a common difference (i.e., ½" or 1"). This creates a stepped effect with headings on each of the signature edges.
Square Tab Format: less conventional format that is generally equal in width and in height (ex. 11" x 11").
Oblong Format: less conventional format that has a longer horizontal axis than a vertical one. It is sometimes referred to as landscape format and is popular for coffee-table books, art books and other applications where standing out is a priority.
To learn more about print formats, contact us.
Binding Techniques
Differentiating various binding techniques can be confusing. Yet making the right selection is important for reasons ranging from durability and utility to appearance and cost. Here is an overview of the most common alternatives and their applications:
Saddlestitching. Bound materials where staples hold the pages together. Signature are automatically gathered one inside the other and secured through the center with two or three staples. Saddlestitching has thickness limitations — generally 1/4" — and lower perceived value.
Perfect Binding. Signature are automatically gathered one on top of the other and glued with a flexible adhesive — EVA, PUR or white (cold) depending upon the use — that holds each page in place after trimming the signature folds along the spine. A popular choice for higher page-count documents because of openability, high-perceived value and affordability. Perfect binding is best suited for either soft- or hard-cover print materials at least 1/4" thick.
Layflat. A variety of perfect binding where a reinforcing strip is applied along the backbone of the cover. The text block is then secured by multiple applications of glue and a bead of pressure sensitive hot melt just above the back edge of both covers. The resulting gap on the spine between the text block and the cover provides flex that enables the document to lay flat when opened.
Case Binding. The ultimate of bookbinding alternatives, case binding is a method of hardcover binding where the case is made separately from the text block and later attached to it. Glued endsheets attach the text pages to its case. Covers, which can be either round or square edges, always extend beyond the edges of the text pages and may be constructed from rigid or flexible boards and covered with a wide range of materials. Case binding is more costly than soft cover but also has superior longevity and greater perceived value.
Thermal Binding. A low-cost binding method often used in conjunction with in-line digital printing systems or as small, tabletop versions used in offices and quick-print shops. This method most commonly applies heat-fused cloth or plastic strips at the document edge to provide a professional appearance and reasonably durable binding that also allows the piece to open flat.
Coil or Comb Binding. An inexpensive binding method whereby slots are punched along the binding edge with a plastic comb, plastic coil, spiral wire or wire-o inserted into the slots. All of the binding materials are available in a variety of colours. This method allows the document to lay completely flat as well as accommodate a variety of different papers and inserts. Ideal for cookbooks, manuals and similar products.
To learn more about binding techniques, contact us.
Paper Stocks
Experienced graphic design and production professionals understand that there is a great deal to know about paper if you want to get the best possible combination of price and performance. A good start is to simply get command of the basic paper types, their characteristics and uses.
Paper in its initial state is uncoated. Although certain grades can be used as is (i.e. newsprint, offset, …), some customers prefer one of its two possible transformations:
- supercalendered paper
- coated paper
Newsprint Paper
Newsprint is the preferred choice for most newspaper publishers because it combines low cost and high strength. It's an uncoated groundwood paper with an average brightness of 56, an off-white cast and consists mainly of wood pulp. It also has the ability to accept four-colour printing inks with final quality that is suitable for the needs of most newspaper advertisers.
Offset Paper
Offset paper is an uncoated paper with an average brightness between 88 and 96. It has reasonable rigidity, good opacity and a smooth surface, giving excellent printing results even over long runs. An example of a paper in this category is Enviro 100, which is a recycled paper containing 100% post-consumer fibre, made from de-inked pulp and is FSC certified.
Supercalendered Paper (SNC/SCB/SCA/SCA+/SCA++)
One way of making paper easier to print on is using steel rollers (also called calenders) to apply pressure and heat to the paper. The calenders can be either hot or cold depending on the desired texture. The more calenders the paper goes through, the thinner and glossier it becomes. SNC paper usually goes through two sets of calendar rolls and has a gloss level of 63. SCA+/SCA++ paper goes through five or more sets of rolls, thus achieving a gloss level of up to 73. One existing trend is to use supercalendered papers (ex. SCB+) for special sections inside a newspaper
The Supercalendering Process
Coated Paper
About 40% of papers used for printing and writing are coated. Coated paper is divided into two sub-categories: coated groundwood and coated freesheet. In both cases, the base paper is coated with a latex pigment to impart certain qualities to it. This transforms the rough and macro-porous surface of the paper into a more uniform one to improve certain characteristics (gloss, for example) and the final printing quality. After the coating has been applied, calenders are used to impart the surface characteristics (finish) to the paper. This finish can either be gloss, dull, satin or matte.
To learn more about paper stocks, contact us.
Paper Characteristics
What characteristics should you consider when choosing paper for your printed product? Here are the four main criteria that will help you choose paper for routine as well as special projects.
Brightness
Brightness refers to the percentage of light that is reflected back to the eye. A perfectly bright paper would be rated 100%.
Brightness varies according to paper category. For example, newsprint brightness usually ranges from 56 – 59. Optical brighteners such as fluorescents increase brightness. Bright sheets contrast with shaded areas and show the most clarity.
Gloss
Gloss is an optical property of a surface to reflect light in a specular (mirror-like) direction. It is one of a number of important parameters that are used to describe the visual appearance of a printed piece. The factors that affect gloss are the refractive index of the material, the angle of incident light and the surface topography.
Opacity
Opacity is the ability of paper to prevent show-through, which is measured as a percentage of the amount of light that passes through a sheet of paper. Most papers fall between 88 and 98 % opacity.
Caliper, filler and brightness all affect opacity.
- Thick paper is more opaque than thin.
- Rough paper is more opaque than smooth.
- Dark paper is more opaque than light.
Caliper
The caliper of a paper will vary according to the basis weight and the finish of the paper. For example, a 30 lb. paper will be thicker than a 27 lb. paper for the same paper category, assuming the finish is the same for both. And a calendered paper will be thinner, since it has been squeezed between the calenders.
Book manufacturers tend to express the thickness of a paper in pages per inch (PPI). This is because papers of the same weight can have fairly dramatic differences in thickness. 50 lb. book papers, for example, can vary from 310 to 800 pages per inch, depending upon how it is made. Thickness can obviously affect a variety of important factors from the appearance of the final product to how many copies can fit into a truck or onto a display.
Basis Weight and M Weight
Don't feel bad if you find paper weights confusing, especially when you move from one grade to another – like bond to offset. The key point is that all paper is based on the weight of 500 sheets of paper (a ream) cut to a given standard size for that particular grade. The tricky part is that the standard size can change from grade to grade as well as with cover stocks. Here is more information and a guide to help you conquer the paper weight issue.
Adding further complexity to the weight issue is the introduction of foreign-manufactured papers that use the metric system to determine basis weight. In this system, it is the weight of one square meter of paper expressed as grams per square meter or g/m2. Basis 60# in the North American system means that 500 sheets 25" x 38" of 60 lb. book paper weigh 60 pounds. The metric equivalent of the same paper is 89 g/m2.
M weight is the weight for 1,000 sheets. For example, newsprint paper 60M means that 1,000 24" x 36" sheets weigh 60 lb.
To learn more about paper characteristics, contact us.
Colour Gamuts
You're likely using more colour than ever and, according to information presented by Xerox, here's why:
- Customers pick up a full colour mailer first 55% of the time.
- Colour documents are up to 80% more likely to be read.
- Colour increases comprehension by up to 73%.
- Information is located 70% faster when it's in colour.
- Colour improves brand recognition by up to 80%.
What you need to know is that the range of colours, or colour gamut, which can be reproduced on any device or system differs. The visible colour gamut is largest, while the red, green and blue (RGB) colour gamut of computer devices is next and the cyan, magenta, yellow, black (CMYK) of printing devices and systems is the smallest. What this means is that as each colour gamut narrows, there are fewer colours that can be reproduced accurately from the visual spectrum. So a computer cannot reproduce all the colours you can see visually and a printing device cannot reproduce all the colours that you can see on the computer screen.
The solution is end-to-end colour management systems that incorporate digital cameras, colour scanners, monitors, proofing devices and printing presses. This involves calibrating the inherent physical characteristics of all the hardware used in your colour reproduction stream and keeping it within the expected boundaries. You'll also need to create profiles of each device so that what you see on your screen is possible to reproduce. Your printer can help.
Matching Pantone(R) Colours in CMYK
Some offset presses and most digital presses have 4-colour capabilities only. In those instances, you'll need to create Pantone(R) spot colours in their CMYK equivalents. You'll achieve the greatest accuracy by using a Pantone(R) Colour Bridge guide, which shows the actual Pantone colour and the CMYK blend side-by-side. You may notice that colours with reflex blue in their colour formula do not reproduce well in CMYK. So if one of these colours is a sensitive corporate colour, you'll want to be especially cautious.
To learn more about colour gamuts, contact us.
Recycled Paper and Certified Paper
A common point of confusion involves the difference between forestry-certified and recycled paper.
First, recycled paper is not necessarily certified paper and vice versa. Recycled paper contains a percentage (up to 100%) of pre-consumer and/or post-consumer recycled fibres. Conversely, certified papers can be made from a combination of:
- Virgin fibre certified according to the principles of sustainable development
- Recycled fibre
- Virgin fibre whose provenance is controlled
Multi-stream recycling is the norm in North America. This means that all recycled materials (glass, plastic, paper, etc.) are mixed at the beginning and then sorted afterward. This increases the risk of contamination of the materials and affects the ultimate quality of what can be used to produce recycled paper. This, in turn, has affected the price of recycled fibre, which has risen considerably over the past few years.
Another consideration is that the use of recycled fibre in the paper affects its brightness: the higher the percentage of recycled fibre, the greyer the paper looks. Very little paper is easily available with a high percentage of recycled fibre.
Certified paper consists of an independent, third-party assessment of sustainable forest management against preset standards. These programs address issues such as biodiversity, protecting species that are at risk and protecting water quality. The organizations perform independent audits and make their summary results publicly available. Multiple stakeholders generally participate in setting standards and programs, incorporating complaint and appeals processes.
Although there are more than 50 certification programs worldwide, the most common in North America are:
- Forest Stewardship Council (FSC)(R)
- Programme for the Endorsement of Forest Certification (PEFC)TM
- Sustainable Forest Initiative (SFI)(R)
- Canadian Standards Association (CSA)(R)
Printers play a key role in the chain of custody aspect of certification programs. Best practices demand that each link in the chain (forest, paper mill and printing facility) must be validated with a Chain of Custody (CoC) certificate in order to apply the appropriate forestry certification logo on the printed product. A certified logo on a printed product means that the paper has been manufactured using pulp from forests that have been managed in a sustainable manner, that the sources are verifiable and that the paper has been properly handled through the supply chain.
All of TC Transcontinental Printing's facilities are triple-certified. This means that when a customer requests certified paper, the applicable logo can be printed, from either Forest Stewardship Council (FSC)(R), Sustainable Forestry Initiative (SFI)(R) or Programme for the Endorsement of Forest Certifications (PEFC)TM. Each certification is a reflection of the forest's ecological, social and economic diversity.
To learn more about recycled paper and certified paper, contact us.